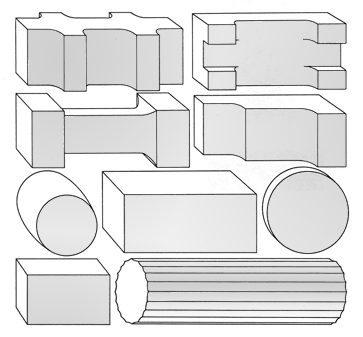
Hand forgings are most commonly produced in simple shapes such as squares, rectangles, biscuits and multi-faced rounds.
Hand forgings classified as standard shapes are squares, rectangles, biscuits and rounds. However, when more complex forging would save later machining costs and enhance the metallurgical and mechanical properties of a part, it is often desirable to produce custom hand forgings embodying more complex design.
In such cases, the internal metal structure can be controlled to a remarkable degree with an appropriately designed, contoured hand forging. Besides saving metal and improving mechanical properties, contoured hand forgings may permit heat-treating and aging operations to be performed without intermediate machining, since sections of such forgings can be made to fall within thickness limits that allow heat treatment for optimal properties.
Standard-shape hand forgings can be described without the aid of a drawing. The predominant direction of grain flow is normally longitudinal in squares, rectangles and multi-faced rounds. In-biscuits, the predominant grain flow is usually radial.
Specialty Shapes
When a hand forging must closely approximate the shape of a finished part, or when machining or metallurgical considerations warrant the use of special techniques, more complex contoured shapes may be fabricated.
Such special shapes may provide maximum directional properties and may substantially reduce machining costs or may even eliminate the expense of regular forging dies. Please submit your drawings or specialty requirements.
When special grain flow characteristics are required, this should be noted in the part specification at time of inquiry. Contoured hand forgings require drawings for their proper description and may be shaped by forging, sawing or machining, or a combination of these methods. They are closer to the configuration of the finished-part design than is ordinarily the case with standard shapes. Contoured hand forgings eliminate considerable subsequent machining time. The shapes may vary widely in complexity. In general, the contoured hand-forging process is facilitated by keeping tapers and bosses symmetrical. Small recesses, holes and notches are left full-to be subsequently machined by the customer. As a contoured hand forging increases in complexity, the cost per pound generally rises.
However, such designs can easily save enough metal and subsequent machining time to compensate for the initial extra cost many times over. In contoured shapes the stock is often worked to lighter sections, so that better mechanical properties may be achieved.